Choosing the right DC motor for your application can feel overwhelming—especially with so many motor types, specifications, and variables to consider.
But once you understand the key performance factors, it becomes much easier to make a confident, informed choice. Whether you’re an engineer, project lead, or purchasing manager, this guide will walk you through the core principles of DC motor selection.
Understanding Voltage, Speed, and Torque
Three parameters form the foundation of any DC motor selection: voltage, speed, and torque. Once you know these, you can begin narrowing down the options.
The goal is to find a motor that operates near its peak efficiency while matching your load and duty cycle requirements.
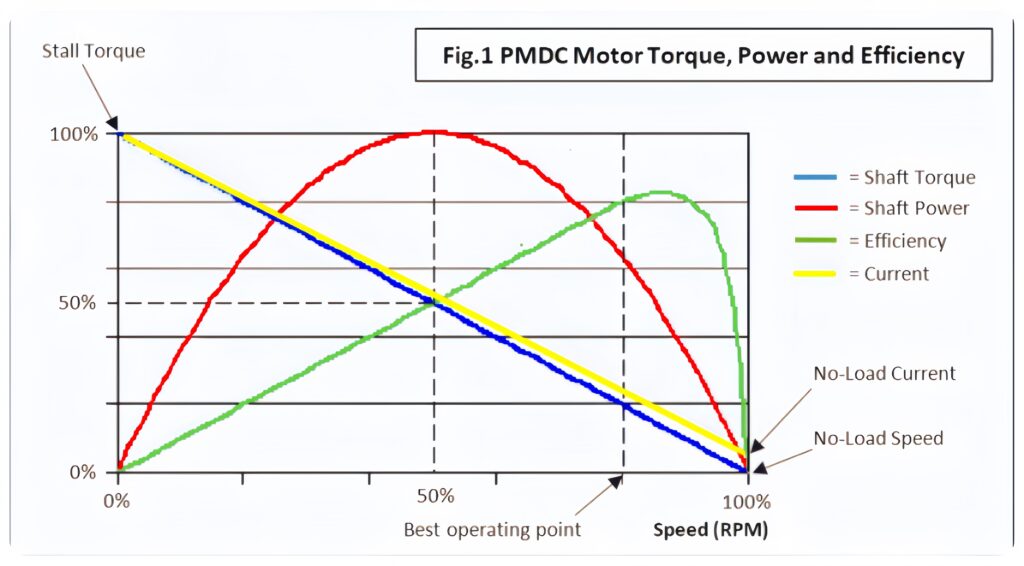
Step-by-Step DC Motor Selection Guide
Step 1: Define Torque and RPM Requirements
Torque is the rotational force the motor must produce. RPM (revolutions per minute) determines how fast the motor turns. A good motor selection balances both—meeting load demands without overworking the system.
Step 2: Consider the Operating Environment
Temperature, humidity, and exposure to dust or chemicals can affect motor lifespan. Harsh environments may require motors with higher IP ratings, special insulation, or additional cooling features.
Step 3: Evaluate Size and Mounting Constraints
Make sure the motor fits within the available space and works with your mounting system. Compact or gear-integrated motors can often simplify installation.
Step 4: Assess Duty Cycle and Load Profile
Will your motor run continuously, start and stop frequently, or handle intermittent bursts? Motors used in high-frequency or high-load conditions need to be more durable.
Step 5: Factor in Energy Efficiency
High-efficiency motors (especially BLDC or EC types) help reduce power consumption over time—especially for applications that run continuously.

How to Specify a DC Motor for Your Application
When specifying a DC motor, consider the following:
Specification | Description |
---|---|
Voltage | Match the motor to your available power supply. |
Speed | Make sure it meets your minimum RPM requirement. |
Torque | Ensure the motor can drive your load without overstrain. |
Key Factors to Consider During Motor Selection
Factor | Description |
---|---|
Speed Stability | Is constant or variable speed control required? |
Torque Requirements | Based on load type (lifting, pushing, rotating, etc.) |
Duty Cycle | Continuous vs. intermittent operation |
Load Compatibility | Confirm mechanical load and motor compatibility |
Maintenance Needs | How easy is it to service or replace the motor? |
Power Source | Confirm voltage/current compatibility with your system |
Lifetime Expectations | Will the motor meet lifecycle requirements? |
Enclosure Rating | Choose IP ratings based on environment |

Where Are DC Motors Used?
DC motors are widely used in industries that require precise control, quiet operation, or compact design:
Application | Typical Use Cases |
---|---|
Robotics | Servo control for arms, AGVs, and autonomous navigation |
Automotive | Wipers, seats, power windows, and electric drive systems |
Industrial Equipment | Conveyor belts, pumps, valves, fans |
Smart Home Devices | Curtains, vacuum robots, smart locks |
Medical Equipment | Infusion pumps, prosthetics, diagnostic tools |
Aerospace Systems | Actuators, satellite positioners, onboard robotics |

Summary
Selecting the right DC motor requires balancing torque, speed, voltage, environment, and expected lifespan. Once you define your application’s key requirements, you can confidently choose a motor that ensures long-term performance and efficiency.
Get Help with DC Motor Sizing →
Related Articles:
- Brushed vs Brushless DC Motors – Key Differences
- How DC Motors Work – A Beginner’s Guide
- How to Control the Speed of a DC Motor
- How Many Types of DC Motors Are There?
- DC Motor Maintenance – 10 Essential Tips
- Why Use DC Motors in Home Automation?
Or explore: